Featured in Bridging & Financial. Written by SIMON THOMPSON.
To Plug the UK's housing shortfall, our government will need to put all the resources which are on offer towards its goal of 3000,000 new homes per year by the mid-2020s.
As part of this, Esher McVey, minister of state of housing and planning, has pledged to bring modern methods of construction (MMC) to the forefront and make the country a world leader in modular building within the next 10 years.
Set to be a monumental growth area, we take a look at innovations in the property development sphere which are slowly coming to the surface, and get a feel for whether they could truly disrupt traditional approaches.
3D - PRINTED HOMES
3D-printed houeses are made out of cement sand and additives, and constructed through incremental printed layers placed upon one another. The construction is delivered by a pre-mapped trajectory and managed through computer-modelling.
According to Constructions-3D—a French company which specialises in these solutions—automated printed systems mean that buildings can be completed extremely quickly, with minimal manpower.
Dini Enrico, CEO atD-Shape—a business in Italy which focuses on the design of 3D-printed homes—adds that it can also eliminate uncertainties in the interpretation of drawings.
With an automatic construction system, the execution times are said to be reduced by 25%. 3D-technology companies, such as Constructions-3D, primarily concentrate on printing the building’s frame structure sand revert to traditional methods when it comes to roofs and fittings.
D-Shape’s building technique is used to print a house in its entirety—from the foundations up to the roof. There are a number of environmental benefits associated with 3D-printing, such as the reduction of onsite logistics resulting in less waste due to only one material being used.
In the long term, this technology is expected to allow house builders to utilise local materials leading to a reduced carbon impact and lower ratio of cement used. In terms ofend-user energy use, more flexibility in designs could allow for higher levels of heat retention and more efficient cooling. With this method of house building still at an early stage of development, it does face ongoing challenges.
Dini notes that weather conditions can complicate 3D-printing operations. In the same vein, Dini claims the interdisciplinary nature of mixing robotics and cement can make it hard to find digitally skilled carpenters.
While there is not much progress currently in the3D-printed housing space in the UK, it is a MMC with the potential to enhance the speed and sustainability of house building in the future.
PANELISED MODULAR BUILDING SYSTEMS
Panels are manufactured and then transported to construction sites, where they are clicked and glued together to form the fabric of buildings. The components can be delivered in bulk to construct homes of any shape and size. Steve Wilkie, director at modern house builder Built & Spaces,says this means there are few restrictions in terms of the types of buildings and designs for the end user.
“The same systems can be applied to all kinds of dwellings and office space, giving it huge flexibility. Extra rooms can be added at the click of a button,offering unparalleled customisation.” This is in contrast to entirely prefabricated housing, which can only be as wide as the road that will carry them to their final destination, according to Joseph Daniels,CEO at modular developer Project Etopia.
The key benefit of using panels is faster build times. They can often be assembled to create a house in a much shorter time frame compared with conventional bricks-and-mortar homes. Steve adds that Built & Spaces can deliver a project that would traditionally take 18 months in as little as eight weeks. With regard to the environment, he explains that its component-led system can dramatically reduce the amount of waste created during manufacture and construction.He claims that the construction of a one bedroom, new-build house can produce 6.5 tonnes of waste on average, while its property creates just 65kg.
“Everything we do is about minimising waste and adding value to every home.” Steve argues that panelised systems are key to meeting the government’s new-build targets. He claims that modern house builders are faster, more efficient and can deliver a higher-quality product for the same cost, compared with traditional developers.
“We have no interest in artificially keeping property prices sky high,” he adds. However, Joseph notes that because the technology is so new, it is difficult to prove that MMC homes can last the hundreds of years that traditional houses have. “This can make it harder to demonstrate to funders that they are investing in a product that lasts as long as the houses they usually invest in.”
The Building Research Establishment’s (BRE)development of a new certification standard for modular homes could be a watershed moment for the off-site construction industry. Joseph says this could go a long way towards addressing funders’ concerns.
SCREW PILING
Screw piles are a steel ground an choring system used for building deep foundations,as a substitute for traditional concrete on low-rise buildings. This can be rapidly installed with the volume of labour required massively reduced compared with traditional methods. It sidesteps the need,expense and skill of machinery—such as excavators, dump trucks, concrete wagons and mixers—which are a prerequisite for conventional foundations.
Richard Thompson, head of construction at Platinum Rise Capital Partners, explains that this can also lead to major eco benefits, as concrete, which is used in the foundations of many developments, has far-reaching negative environmental impacts. Due to the fact that screw piles can be driven much closer and through tree route systems, it is said to support the conservation of trees,as concrete footings often damage roots.
Richard claims that, in some cases, they can even be installed using a hand-held piling machine, depending on the size of the development. Although there isn’t an initial cost benefit, the main advantage is the time saved, leading to a quicker return on the building. Richard claims that the key challenges to its broader use in the UK is less about quality and feasibility, and more about how it is perceived.
“The challenge is educating the industry [about] this technology and promoting the benefits. It is more common on low-rise buildings and isn’t seen as an alternative to concrete piles on large commercial developments.”Edward Clark, managing director at Uplift Finance, says he is seeing more deals involving MMC. He claims that lenders’reluctance to fund such deals is due to unfamiliarity.
“There’s a difference between risk and the unknown. Banks don’t like the unknown. But risk can be observed and measured; it can be priced in.” He explains that as knowledge and awareness increases,the various risks of MMC can be defined—and then “you can mitigate them”.
CROSS-LAMINATED TIMBER
Cross-laminated timber (CLT) is formed using small sections of timber bonded together with permanent adhesives.Imperfections, such as knots, are removed in the factory to reduce variability and enhance structural performance. It is formed into panels through layers glued perpendicularly to each another to deliver strength across two dimensions.
Akeel Malik, fund manager at Urban Splash Residential Fund, says it uses CLT in some of its developments. While Akeel believes it is too early to measure the cost advantages of building with it, the quality and eco benefits are already obvious.
“In terms of end use, CLT is a much more sustainable material than traditional options,like steel and concrete, thanks to the fact that it’s ideal for insulation, retaining heat in the winter and letting the building breath in the summer. Inevitably, we’ll face challenges as we move forward, but right now it’s a really impressive material to use.”
He says there will need to be more confidence in and uptake of it if UK housing is to see the benefits of broader adoption.Edward has arranged a handful of deals using CLT. “To do them, you have to fund the deposit for the build yourself.And you may need to use a lender with a very high interest rate. I’ve seen it double from 6% to 12%.”
He speculates that with the coming sea change in construction methods and eco-minded initiatives,being traditional may not be the secured,favoured option for much longer.
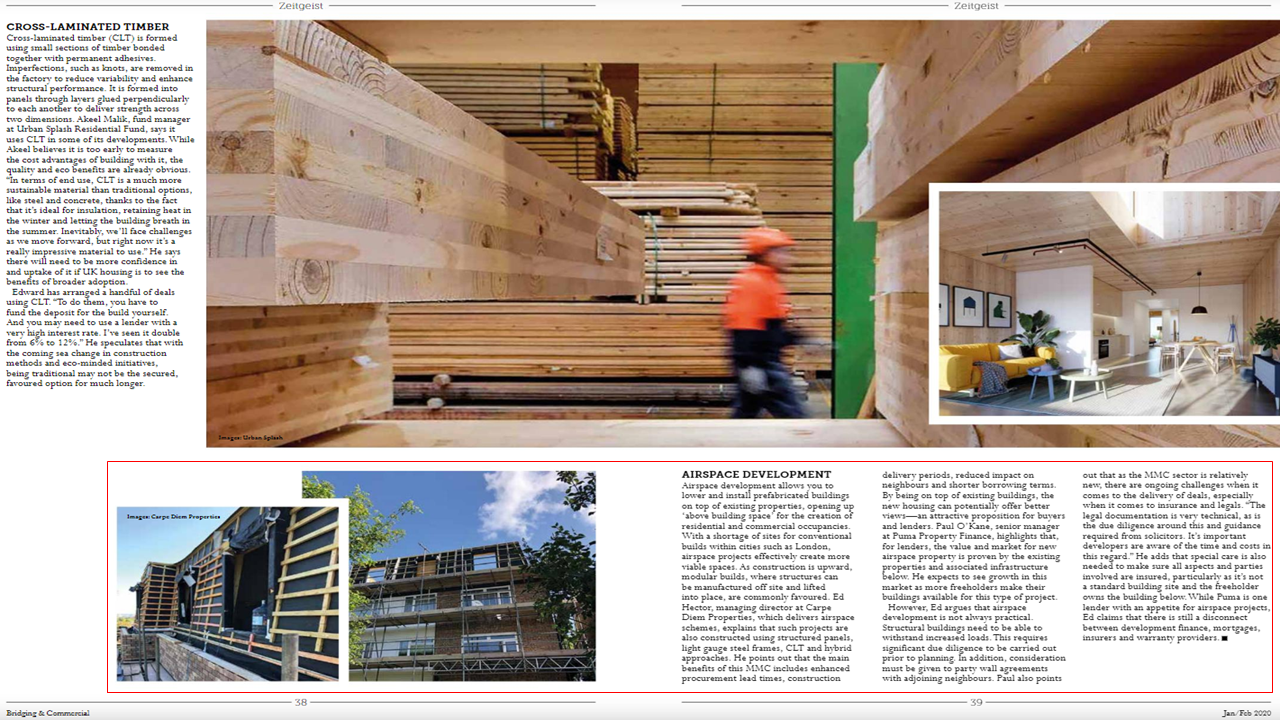
AIRSPACE DEVELOPMENT
Airspace development allows you to lower and install prefabricated buildings on top of existing properties, opening up‘above building space’ for the creation of residential and commercial occupancies.
With a shortage of sites for conventional builds within cities such as London,airspace projects effectively create more viable spaces. As construction is upward,modular builds, where structures can be manufactured off site and lifted into place, are commonly favoured.
Ed Hector, Managing Director at Carpe Diem Property, which delivers airspace schemes, explains that such projects are also constructed using structured panels,light gauge steel frames, CLT and hybrid approaches.
He points out that the main benefits of this MMC includes enhanced procurement lead times, construction delivery periods, reduced impact on neighbours and shorter borrowing terms.
By being on top of existing buildings, the new housing can potentially offer better views—an attractive proposition for buyers and lenders.
Paul O’Kane, senior manager at Puma Property Finance, highlights that,for lenders, the value and market for new airspace property is proven by the existing properties and associated infrastructure below. He expects to see growth in this market as more freeholders make their buildings available for this type of project.However, Ed argues that airspace development is not always practical.
Structural buildings need to be able to withstand increased loads. This requires significant due diligence to be carried out prior to planning. In addition, consideration must be given to party wall agreements with adjoining neighbours.
Paul also points out that as the MMC sector is relatively new, there are ongoing challenges when it comes to the delivery of deals, especially when it comes to insurance and legals. “The legal documentation is very technical, as is the due diligence around this and guidance required from solicitors. It’s important developers are aware of the time and costs in this regard.”
He adds that special care is also needed to make sure all aspects and parties involved are insured, particularly as it’s nota standard building site and the freeholder owns the building below.
While Puma is one lender with an appetite for airspace projects,Ed claims that there is still a disconnect between development finance, mortgages,insurers and warranty providers.